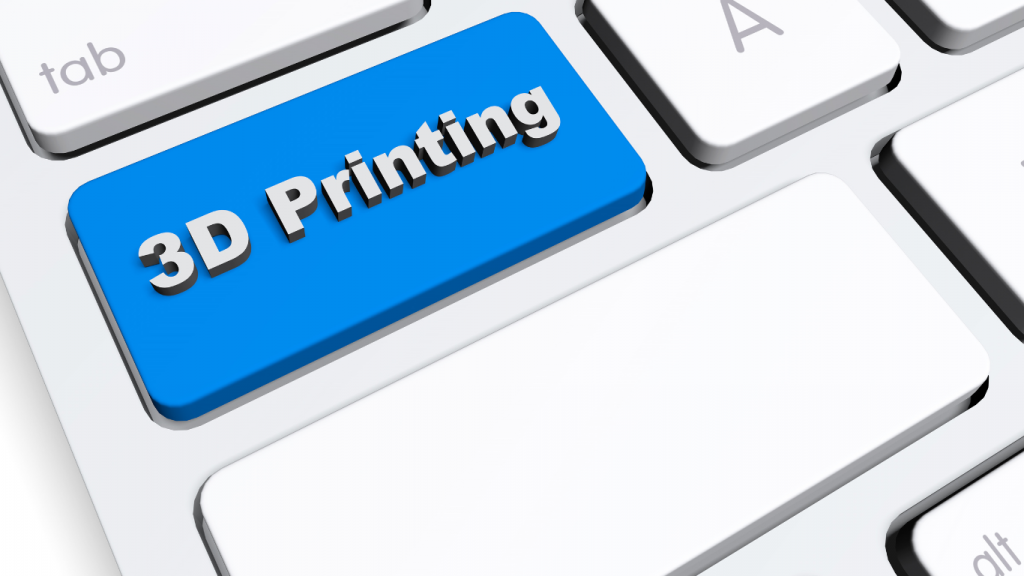
3D drug printing
In an era where personalization is permeating every facet of our lives, from tailored news feeds to custom-crafted diets, the pharmaceutical industry is undergoing a transformation of its own. Enter 3D drug printing—a technology poised to revolutionize how we develop, manufacture, and administer medications. While it offers promising benefits, it also presents challenges that need to be addressed to realize its full potential.
The Benefits of 3D Drug Printing
1. Personalized Medicine: One of the most significant advantages of 3D drug printing is the ability to create medications tailored to individual patient needs. By adjusting dosages, combining multiple drugs into a single pill, or customizing drug release profiles, healthcare providers can offer treatments that are more effective and have fewer side effects.
2. On-Demand Manufacturing: 3D printing enables the production of drugs on-demand, reducing the need for large inventories and allowing for rapid response to urgent medical needs. This is particularly beneficial in remote areas or during emergencies where immediate access to medications is critical.
3. Complex Drug Formulations: Traditional manufacturing methods can struggle with producing complex dosage forms. 3D printing allows for the creation of intricate drug geometries and release mechanisms, improving therapeutic outcomes and patient adherence.
4. Reduction in Waste: By producing only what is needed, 3D printing minimizes material waste. This not only has environmental benefits but can also reduce costs associated with the disposal of expired or unused medications.
5. Improved drug stability: Customization can extend to the excipients used, potentially enhancing the stability of drugs that are sensitive to environmental conditions.
Limitations for Scalability
1. Production Speed: Current 3D printing technologies are relatively slow compared to traditional high-throughput pharmaceutical manufacturing processes. Scaling up production to meet the demands of large populations remains a significant challenge.
2. Regulatory Hurdles: The regulatory framework for 3D printed drugs is still evolving. Ensuring quality control, consistent dosing, and adherence to Good Manufacturing Practices (GMP) is more complex with decentralized and customized production.
3. Equipment and Maintenance Costs: High initial investment in 3D printing equipment and the ongoing costs of maintenance and validation can be prohibitive, especially for smaller healthcare providers or in resource-limited settings.
4. Material Limitations: Not all pharmaceutical compounds are compatible with 3D printing processes. There is a need for a broader range of printable materials that are safe, effective, and approved for medical use.
5. Skilled Workforce: Operating sophisticated 3D printing equipment requires specialized training. There is a gap in the workforce skilled in both pharmaceutical sciences and advanced manufacturing technologies.
Formulation Challenges
1. Drug-Excipient Compatibility: Ensuring that the active pharmaceutical ingredients (APIs) are compatible with the excipients used in 3D printing is crucial. Incompatibilities can affect drug efficacy and patient safety.
2. Uniformity and Precision: Achieving consistent drug distribution within a printed dosage form is essential. Variations can lead to dosing errors, which can be harmful or reduce treatment effectiveness.
3. Stability of APIs: Some APIs may degrade during the printing process due to heat or other factors. Developing formulations that maintain stability throughout manufacturing is a key hurdle.
4. Controlled Release Profiles: Designing formulations that deliver drugs at the desired rate and time requires careful consideration of the printing process and materials used.
5. Validation and Testing: Each new formulation may require extensive testing to ensure safety and efficacy, which can be time-consuming and costly.
The Futuristic Scope of 3D Drug Printing
Despite the challenges, the future of 3D drug printing is bright. As technology advances, we can anticipate several developments:
1. Integration with Digital Health: Combining 3D printing with digital health records could allow for real-time customization of medications based on patient data, genetics, and lifestyle factors.
2. Hospital Pharmacies as Manufacturing Sites: Hospitals could become mini-manufacturing hubs, producing medications on-site tailored to the immediate needs of their patients.
3. Global Accessibility: Portable 3D printers could provide access to essential medications in remote or under-resourced areas, reducing global health disparities.
4. Innovative Drug Delivery Systems: We may see the creation of novel delivery systems, such as implants or transdermal patches, that are 3D printed to provide targeted therapy.
5. Sustainable Manufacturing Practices: Advancements could lead to greener manufacturing processes with a smaller carbon footprint, aligning with global sustainability goals.
Conclusion
3D drug printing stands at the intersection of technology and medicine, offering a pathway to more personalized, efficient, and accessible healthcare. While scalability and formulation challenges exist, ongoing research and innovation are paving the way for these obstacles to be overcome. As we look to the future, embracing this technology could lead to a paradigm shift in how medications are developed and dispensed, ultimately improving patient outcomes and transforming the pharmaceutical landscape.
Let’s connect and continue the conversation about the future of pharmaceuticals and healthcare innovation. please visit us vanuston also our product pages at medeillcoud